1、 Basic Conversion Relationship
1. Corresponding relationship between power and steam volume
-Steam boiler: 1 ton/hour (T/h) of steam corresponds to a thermal power of approximately 720 kW or 0.7 MW.
-Thermal oil furnace: The conversion between electric heating power (kW) and steam volume needs to be achieved through heat load (kJ/h). For example, if the power of the thermal oil furnace is 1400 kW, the corresponding steam volume is about 2 tons/hour (calculated as 1 ton of steam ≈ 720 kW).
2. Conversion of thermal energy units
-1 ton of steam ≈ 600000 kcal/h ≈ 2.5GJ/h.
-The relationship between electric heating power (kW) and heat: 1kW=860kcal/h, therefore 1400kW electric heating power corresponds to 1.204 million kcal/h (approximately 2.01 tons of steam).
2、 Conversion formula and parameters
1. Calculation formula for electric heating power
\-Parameter description:
-(P): Electric heating power (kW);
-(G): Mass of heated medium (kg/h);
-(C): Specific heat capacity of the medium (kcal/kg ·℃);
-\ (\ Delta t \): Temperature difference (℃);
-(eta): Thermal efficiency (usually taken as 0.6-0.8).
2. Example of steam quantity calculation
Assuming 1000kg of heat transfer oil needs to be heated from 20 ℃ to 200 ℃ (Δ t=180 ℃), the specific heat capacity of the heat transfer oil is 0.5kcal/kg ·℃, and the thermal efficiency is 70%:
\The corresponding steam volume is approximately 2.18 tons/hour (calculated based on 1 ton of steam ≈ 720kW).
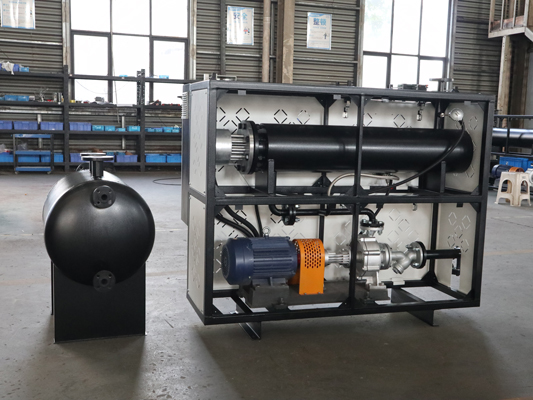
3、 Adjustment factors in practical applications
1. Differences in thermal efficiency
-The efficiency of electric heating thermal oil furnace is usually 65% -85%, and the power needs to be adjusted according to the actual efficiency.
-Traditional steam boilers have an efficiency of about 75% -85%, while electric heating systems have higher efficiency due to the absence of fuel combustion losses.
2. Influence of medium characteristics
-The specific heat capacity of thermal oil (such as mineral oil) is about 2.1 kJ/(kg · K), while that of water is 4.18 kJ/(kg · K), which needs to be adjusted according to the medium for calculation.
-High temperature conditions (such as above 300 ℃) require consideration of the thermal stability of the heat transfer oil and system pressure.
3. System design margin
-Suggest adding a safety margin of 10% -20% to the calculation results to cope with fluctuating loads.
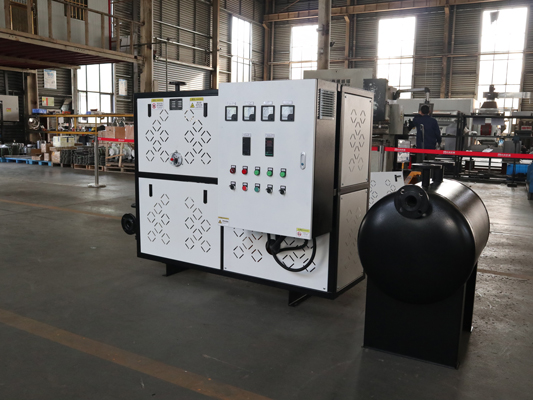
4、 Typical Case Reference
-Case 1: A traditional Chinese medicine factory uses a 72kW electric steam generator, corresponding to a steam volume of approximately 100kg/h (calculated as 72kW × 0.7 ≈ 50.4kg/h, actual parameters need to be combined with equipment nameplates).
-Case 2: A 10 ton thermal oil furnace (with a power of 7200kW) heats up to 300 ℃, with an annual power consumption of approximately 216 million kWh and a corresponding steam volume of approximately 10000 tons per year (assuming 720kW=1 ton of steam).
5、 Precautions
1. Equipment selection: Accurate selection should be made based on process temperature, medium type, and heat load to avoid insufficient power or waste.
2. Safety regulations: The insulation performance of the electric heating system needs to be checked regularly, and the pressure and leakage risk of the steam system need to be monitored.
3. Energy efficiency optimization: The electric heating system can further save energy through frequency conversion control and waste heat recovery.
For specific equipment parameters or customized calculations, it is recommended to refer to the manufacturer's technical manual or contact professional technicians.
If you want to know more about our product, please contact us!
Post time: May-16-2025