To meet the high requirements of customers for water pressure and air pressure in the design of flange electric heating tubes, comprehensive optimization is needed from multiple dimensions such as material selection, structural design, manufacturing process, and performance verification. The specific plan is as follows:
1、 Material selection: Improve compressive strength and sealing foundation
1. Selection of main pipe materials
High strength and corrosion-resistant materials are preferred for high-pressure working conditions (water pressure ≥ 10MPa or air pressure ≥ 6MPa), such as:
Stainless steel 316L (resistant to general corrosive media, compressive strength ≥ 520MPa);
Incoloy 800 (resistant to high temperature, high pressure and oxidation, suitable for high temperature steam environment, yield strength ≥ 240MPa);
Titanium alloy/Hastelloy alloy (for highly corrosive and high-pressure media such as seawater and acid-base solutions).
The wall thickness of the pipe is calculated according to the standards of GB/T 151 Heat Exchanger or ASME BPVC VIII-1, ensuring a wall thickness margin of ≥ 20% (such as calculating the wall thickness+0.5mm safety factor when the working pressure is 15MPa).
2. Flange and seal matching
Flange type: In high-pressure scenarios, neck welding flanges (WNRF) or integral flanges (IF) are used, and the sealing surface is selected as mortise and tenon (TG) or ring joint (RJ) to reduce the risk of sealing surface leakage.
Sealing gasket: Choose metal wrapped gasket (with inner and outer rings) (pressure resistance ≤ 25MPa) or octagonal metal ring gasket (high pressure and high temperature, pressure resistance ≥ 40MPa) according to the characteristics of the medium. The gasket material is compatible with the pipe material (such as 316L gasket with 316L flange).
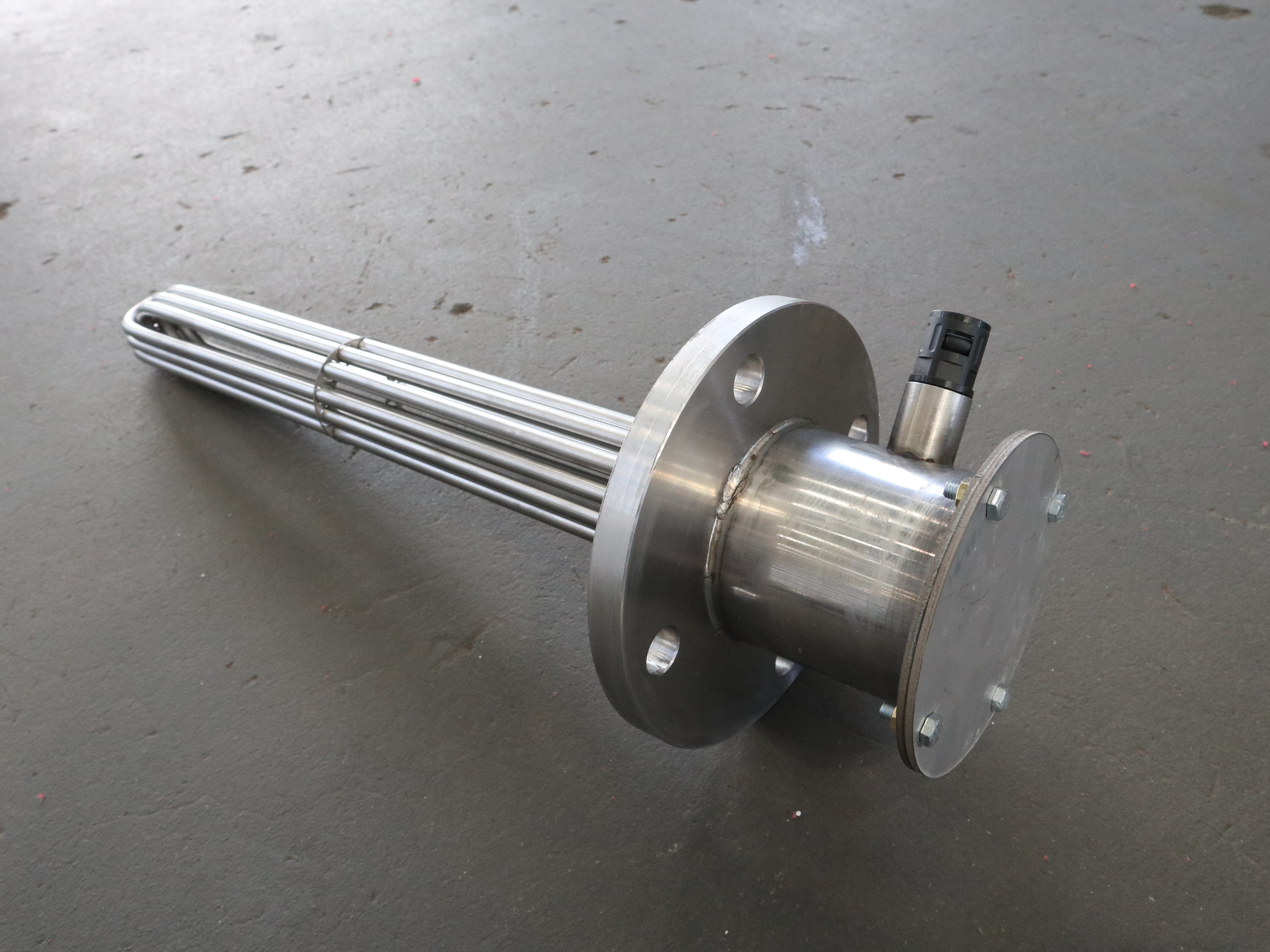
2、 Structural Design: Strengthening Pressure and Reliability
1. Mechanical structure optimization
Bend design: Avoid right angle bending and use a large curvature radius (R ≥ 3D, D is the pipe diameter) to reduce stress concentration; When laying out multiple pipes, they are symmetrically distributed to balance radial forces.
Strengthening structure: Add support rings (spacing ≤ 1.5m) or built-in central positioning rods to the long straight heating tube to prevent deformation of the tube body under high pressure; The connection section between the flange and the pipe body adopts a thickened transition zone (gradient groove welding) to enhance the tear resistance of the weld seam.
2. Sealing and connection design
Welding process: The pipe body and flange are fully penetrated welded (such as TIG welding+filler wire), and 100% X-ray testing (RT) or penetration testing (PT) is performed after welding to ensure that the weld seam is free of pores and cracks;
Expansion assistance: The heat exchange tube is connected to the tube plate using a dual process of hydraulic expansion and sealing welding. The expansion pressure is ≥ twice the working pressure to prevent medium leakage from the tube plate holes.
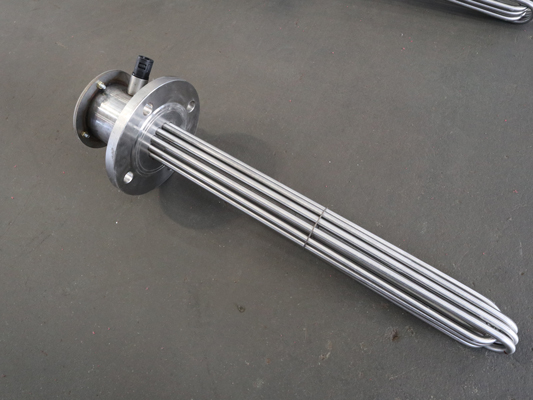
3、 Manufacturing process: strict control of defects and consistency
1. Control of machining accuracy
The pipe cutting adopts laser/CNC cutting, with end face perpendicularity ≤ 0.1mm; flange sealing surface roughness ≤ Ra1.6 μ m, bolt hole uniform distribution error ≤ 0.5mm, ensuring uniform force during installation.
Magnesium oxide powder filling: using vibration compaction technology, filling density ≥ 2.2g/cm ³, to avoid local overheating or insulation failure caused by hollow sections (insulation resistance ≥ 100M Ω/500V).
2. Stress testing and validation
Pre factory testing:
Hydrostatic test: The test pressure is 1.5 times the working pressure (such as 10 MPa working pressure and 15 MPa test pressure), and there is no pressure drop after holding for 30 minutes;
Pressure test (applicable to gas media): The test pressure is 1.1 times the working pressure, combined with helium mass spectrometry leak detection, with a leakage rate of ≤ 1 × 10 ⁻⁹ mbar · L/s.
Destructive testing: Sampling is used for explosion pressure testing, and the explosion pressure must be ≥ 3 times the working pressure to verify the safety margin.
4、 Functional adaptation: to cope with complex working conditions
1. Thermal expansion compensation
When the length of the heating tube is ≥ 2m or the temperature difference is ≥ 100 ℃, a waveform expansion joint or flexible connection section should be installed to compensate for thermal deformation (expansion amount Δ L=α L Δ T, where α is the material's linear expansion coefficient) and avoid flange sealing surface failure caused by temperature difference stress.
2. Surface load control
High pressure media (especially gases) are sensitive to local overheating and require a reduction in surface load (≤ 8W/cm ²). By increasing the number or diameter of heating tubes, dispersing power density, and preventing scaling or material creep (such as surface load ≤ 6W/cm ² during steam heating).
3. Media compatibility design
For high-pressure fluids containing particles/impurities, a filter screen (with an accuracy of ≥ 100 mesh) or a guide cover should be installed at the inlet of the heating tube to reduce erosion; Corrosive media require additional surface passivation/spraying treatment (such as polytetrafluoroethylene coating, temperature resistance ≤ 260 ℃).
5、 Standard and customized design
Provide material reports, welding procedure qualification (PQR), and pressure test reports in accordance with national standards (GB 150 "Pressure Vessels", NB/T 47036 "Electric Heating Elements") or international standards (ASME BPVC, PED 2014/68/EU).
To meet the special needs of customers (such as high-pressure heating for API 6A wellhead equipment and deep-sea pressure resistant heating), we collaborate with customers to simulate working conditions (such as finite element analysis of stress distribution and CFD flow field optimization) and customize flange specifications (such as special threaded flanges and sulfur resistant materials).
summarize
Through the full process optimization of "material strength guarantee → structural load resistance design → manufacturing accuracy control → testing and verification closed-loop", the flange electric heating tube can achieve reliable operation under high voltage conditions. The core is to balance the pressure bearing capacity, sealing performance, and long-term stability, while taking into account the characteristics of the customer's medium (temperature, corrosiveness, flow rate) for targeted design, ultimately meeting the safety margin requirement of water pressure/air pressure ≥ 1.5 times the design parameters.
If you want to know more about our product, please contact us!
Post time: May-09-2025